Process
1 - Engineering
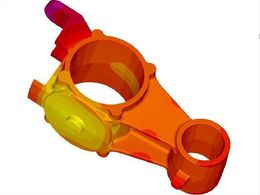
From the beginning, we collaborate with our clients in the analysis and finalisation of the drawings aimed at the correct execution of the casting with the right containment of the production cost. We make use of the SOLID CAST programme for the simulation of the cooling of the casting cluster. Before the production of the batches, a sampling is always carried out in which all the parameters necessary for process control are recorded and any critical issues are highlighted.
3 - foundry
In this department, three fundamental processes take place:
The green moulding process is carried out with a mechanised process that uses 1 Motta system and 1 coreless system. The physical and mechanical properties of the green sand are constantly monitored by an automatic data detection system.
The casting of cast iron takes place in a rotary furnace with an oil combustion system, with a capacity of 8 tonnes; the liquid cast iron is tapped from the furnace and transferred to an electric furnace with a capacity of 12 tonnes, which acts as a buffer between the melting system and the moulding systems. During the transfer operation, analytical controls, thermal analysis, and spectrometric analysis are performed. The molten metal is manually poured into the moulds using small ladles suspended from monorails. For the production of castings in flake graphite cast iron, the metal is transferred from the electric furnace to the pouring ladles, inoculated, and then poured into the moulds. For the production of castings in nodular graphite cast iron, the metal is transferred into a treatment ladle